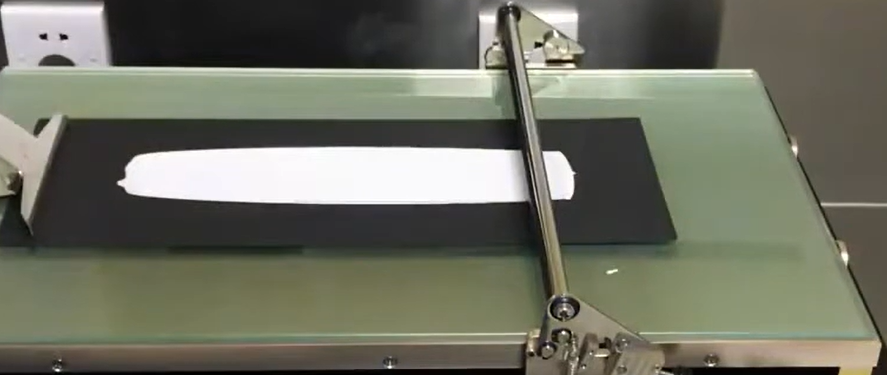
A wire bar coater, also called a K coater, is a significant instrument that finds its application in the printing industry, paper manufacturing, and R&D departments. It uses the traditional method of coating that is widely used for coating paints, printing inks, paints, adhesives, and varnishes on varied surfaces. Printers and paper manufacturers often use it to produce repeatable samples quickly and precisely.
How does a K coater or Wire Bar Coater work?
Before we learn about the functionality of the coater, let us look at its essential characteristics.
Essential Features of a K Coater
- A laboratory K coater is a motorized unit that consists of an offset blanket mounting on it. The standard coating area of the offset blanket is 27 cm x 15 cm.
- It uses the traditional coating method to coat at a controlled velocity and pressure. With the controlled specifications, it can perform uniform and repeated coating.
- The coating is performed using wire wound Mayer bars. The Mayer bar is cylindrical, made of steel, and has a wire wound around it. The thickness of the coating layer is determined by the diameter of the wire while the selection of the wire and its diameter is based on the viscosity of the coating material, coat weight or thickness, and coating speed. The applicable surface coating materials are paints, printing inks, adhesives, varnishes, starch, and so on.
- The standard coating speed ranges between 2 and 15 mm per minute.
- The unit comes with 7 coating rods to offer different coating weights or thicknesses.
- More than two coatings can be done in a single operation using the K coater. This enables the user to compare different results.
Functionality of a K Coater
Just like a doctor blading, the user places the printing ink (or paint, varnish, adhesive, etc.) on the substrate. The cylindrical-shaped steel bar has a wire spiraled around it that spreads the poured ink evenly on the substrate. During this coating procedure, the amount of ink or other solution allowed through the gaps between the wire and substrate determines the ink’s thickness.
Benefits of using a Lab K Coater
- Coating via a wire bar coater or K coater is easy and cost-effective.
- The resulting coating is uniform across the substrate.
- Rods of different numbers offer coating of varied thicknesses.
- The drying time can be controlled.
- The coating process is easily scalable. This makes it an ideal instrument for both the manufacturing and R&D sectors.
These are the essential details that you must know about the wire bar coater before investing. UEC is a leading manufacturer, supplier, and exporter of wire bar coaters and other surface coating equipment. If you are in the printing business, investing in reliable instruments like this can be of great value to your business. Drop an inquiry by visiting UEC’s website at www.uecin.com.