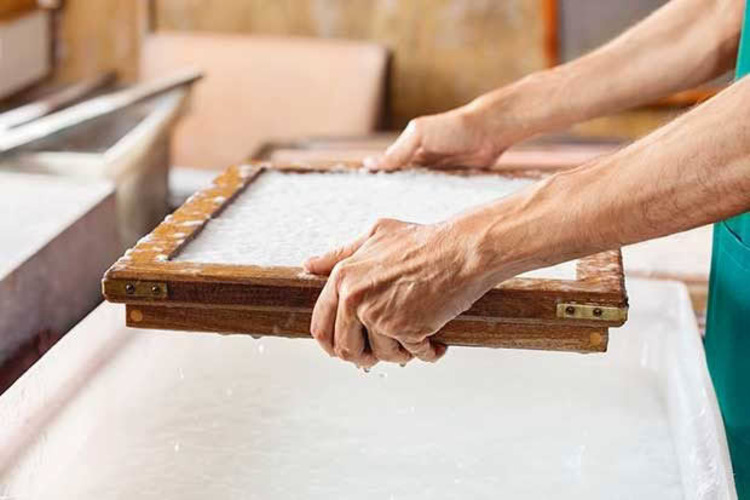
There is a simple explanation as to why forming paper sheets is important: without this process, paper cannot be created. Sheet forming plays a vital role in the manufacturing of paper, as it involves transforming pulp into a consistent sheet. After obtaining pulp stock from a disc refiner, manufacturers use a series of processes to create sheets of desired weight. This is where a sheet pressing machine becomes essential.
What is a sheet pressing machine?
The sheet-pressing machine serves as a tool for pressing and consolidating fibers into a paper sheet. Through the pressing process, the machine effectively eliminates excess water and achieves the desired weight. Afterwards, the sheet is subjected to additional drying to obtain the dried paper sheet.
How does pressing influence the properties of paper?
Pressing is a crucial step in the papermaking process as it helps remove water from the pulp sheet after the initial sheet-forming process. Adequate pressing ensures efficient drying and attainment of the desired paper quality.
The absence of dewatering leads to poor paper quality and performance. Besides, this step has an influence on the surface and physical properties of paper, including printability, porosity, and smoothness.
It also improves the density and strength of the paper as it binds the fibers together. As a result, manufacturers have the flexibility to decide the number of press sections based on the preferred properties of the final paper.
Once the parameters are set, the user must place the stack of sheets centrally in the press. With a simple push-button operation, the pressure is raised and maintained for the set values. On completion, the pressure is released, and the stack can be removed. The sheets should now be firmly attached to the drying platens.
UEC’s lab sheet press performs rapid dewatering of laboratory sample sheets. The press consists of an adjustable press section that houses the press platens. A control panel with two press timers and a pressure regulator allows users to set the desired values.
The unit also comes with a centering template that ensures the laboratory sheets are placed centrally on each other.
Once the settings have been established, the user is instructed to position the pile of sheets centrally in the press. Through a simple push button operation, the pressure is elevated and sustained at the predetermined values.
The paper gets dewatered and up to half of the paper weight gets reduced. Once the process is concluded, the pressure is alleviated, and the stack can be extracted. Subsequently, the sheets are secured to the drying platens and sent for drying.
The Drying stage
In the drying step, the paper sheet or web goes through an effective drying method, typically a sequence of heated cylinders or presses. In the dryer, the temperature is increased to uniformly reduce the moisture content of the paper. It helps the residual water to evaporate. Once the paper dries completely, the user gets the final weight.
The process of sheet forming, pressing, and drying is essential in producing paper with the desired quality and strength. Therefore, paper manufacturers must procure dependable and high-quality pulp and paper testing equipment. UEC offers a comprehensive selection of products to evaluate various properties of your end product.
If you are considering purchasing a lab sheet press, it is likely that you are also interested in other essential pulp and paper testing instruments. To find out more, visit the official website of UEC at www.uecin.com.