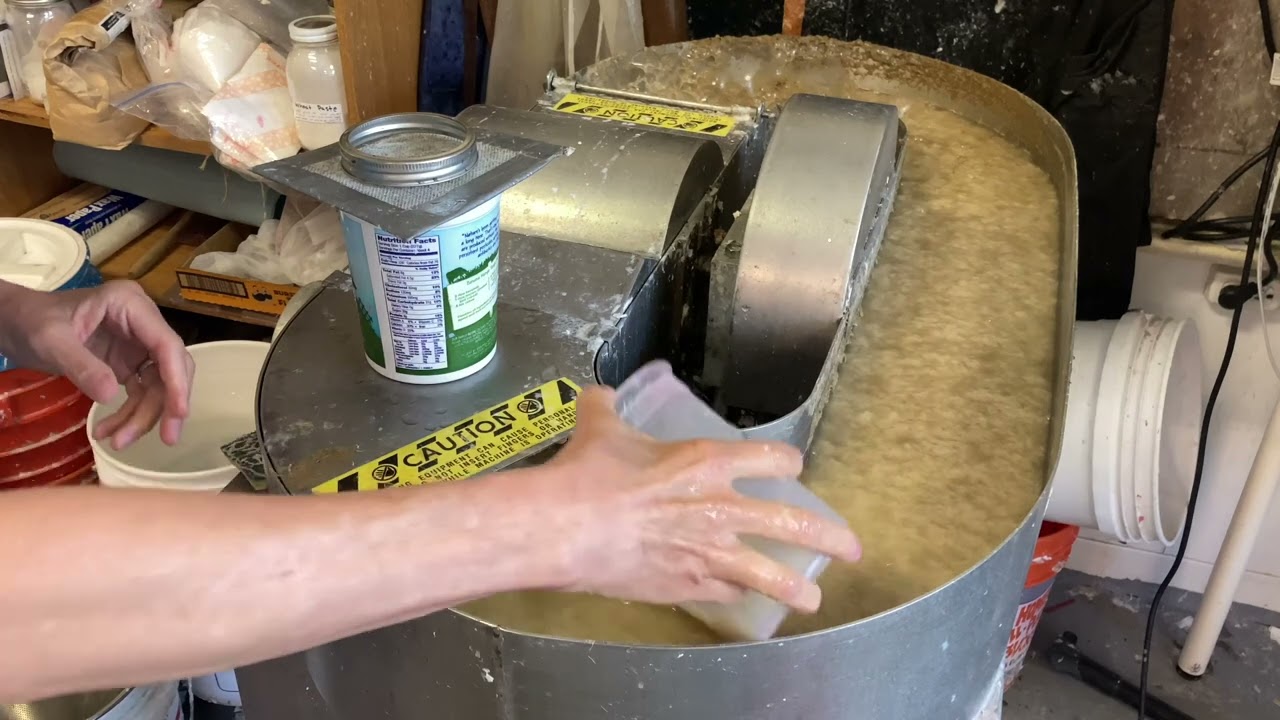
Pulp and paper products are primarily composed of cellulosic fibers derived from wood and other plant sources. However, some papers may incorporate synthetic materials, flax, rags, cotton linters, or bagasse. Additionally, manufacturers often reuse recycled waste paper by purifying and blending it with virgin fibers. Regardless of the raw materials used, the fundamental papermaking process remains consistent, involving a series of steps that include -
- Pulping
- Beating and Refining
- Diluting
- Sheet Forming
- Pressing
- Drying
- Finishing
The primary objective of the pulping process is to separate and purify the wood fibers by removing natural binding components like lignin and hemicellulose. While a pulp digester or a refiner can accomplish this task, the mechanical beating of pulp is essential to produce hydrated and fibrillated fibers, enhancing the strength of the resulting paper.
What is Pulp Beating?
Performed using a Hollander Beater or Valley Beater, pulp beating is the mechanical process that cuts, refines, and fibrillate the wet fibres to improve paper formation. The beating process not only facilitates the dissolution of lignin and extractives but also fosters improved fiber bonding, fundamentally contributing to the production of superior-grade paper and paperboards.
A well-bonded paper is high in strength and thus helps form a robust and smooth paper that also has sound printing characteristics. Moreover, shortening of fibres enhances fiber-to-fiber contact, leading to a denser sheet characterized by superior tensile and bursting strength.
What Happens if The Pulp is Not Beaten?
Once the pulp is cooked, screened, and bleached, it is not immediately suitable for paper production due to its increased elasticity. If it is sent for papermaking in this state, then the resultant paper will have reduced strength and durability.
Moreover, unbeaten pulps contain fibers of various lengths, leading to the production of loose, weak, and coarse paper. Conversely, thorough beating of the pulp results in a stronger and uniform paper structure.
What are the Effects of Beating/Refining on the Pulp?
When the pulp undergoes refining or beating in a beater, it produces the following outcomes:
- Shortening of the fibers
- Straightening or curling of the fibers
- Production of fines
- Removal of parts from the walls of the pulp fiber
- Creation of debris in the suspension
- Internal and external fibrillation. In internal fibrillation, the fibres go through internal changes in the wall structure, such as swelling, delamination, etc. On the other hand, external fibrillation partially removes the fiber wall
- Development and removal of micro-compressions, slip panes, and kinks in and from the cell wall.
- Reduction of the fibre brightness
- Suspension of colloidal material in the external liquor
- Production of a gel-like surface of the fibre with the help of abrasion at the molecular level
How is Pulp Beating Performed in a Hollander Beater?
Hollander Beater has been a significant instrument in the paper industry since the 1600s. It is responsible for producing high-quality pulp possible by improving the fiber properties.
A standard Hollander Beater consists of a motorized unit affixed to a sturdy base frame and includes a tub, rotor, drain valve, roll, bed plate, and cover, each playing a crucial part in ensuring effective beating. The process of beating both cooked and uncooked materials occurs under specified conditions in the following sequence.
- The user puts the pulp into the beater and then adds water to it. The addition of water helps the raw material to circulate between the roll and the bed plate.
- The beater starts as soon as the motorised unit is plugged in. The user gradually lowers the revolving roll until the fibers are cut to the desired length and a uniform mixture is produced.
- The operation is carried out until the entire pulp is processed.
- The result is hairlike fibrils which can further absorb water and are spongy.
Which Hollander Beaters are used in Pulp Beating?
Within UEC's offerings, customers have the choice between two variants of Hollander Beaters.
- A High Capacity Hollander Beater designed for processing 5 to 50 kilograms of oven-dried pulp.
- A Low Capacity Hollander Beater designed for processing 1 to 4 kilograms of oven-dried pulp.
Understanding the purpose and function of Hollander Beaters is essential if you’re looking to invest in them. When considering a purchase, acquiring knowledge about the capacity, pricing, construction material, and functionalities that align with your needs is important.
For further details, do not forget to connect with the experts at UEC who can assist you in making a well-informed decision. Visit our website to explore our range of handmade paper-making machines and testing equipment.